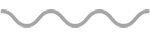
Clamping, Hanging
The galvanizer will use existing holes, handles, fishplates, loops etc. on the object at hanging during the treatment, if they seem to be sufficiently solid and appropriately placed for the galvanizer, but he cannot take the responsibility of any damaging consequences of this. If any risk of this exists, the customer therefore has to warn against it expressly, when he hands in the object for galvanzing.
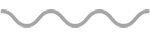
Damage Liability
The galvanizer will take good care of the objects handed in for hot dip galvanizing and treat them in a technically correct way. He will show the necessary watchfulness and care, but will take no responsibility for the results of treating objects which without his knowing are of such a quality that they are damaged or cause damage by treatment. Therefore, when handing in the object for hot-zincing, the customer has to inform the galvanizer sufficiently to enable him to judge and obviate the risk.
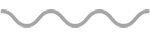
Compound Objects
When objects consisting of more parts are received, the galvanizer will assume that such compound objects are to be treated in assembled condition. The customer ought to take care as per arrangement with the galvanizer that there is enough space between connected surfaces, e.g. in hingers or threads, if the customer wants the parts to be movable after the galvanzing, or threads applicable.
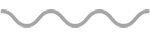
Cleaning, Brushing, Cutting
Cleaning of holes and also cutting or brushing of treads in nuts, bolts or the like will be charged extra and will only be performed according to preceding agreement. The objects must be free from burrs from cuttings, bad clipping, and wire pieces from welding.
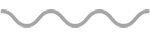
Covering
Every surface part, which should not be galvanized, has to be stated clearly in the order. Covering of such surfaces will bet charged extra. However, the placing or extent of a surface might prevent its effective covering.
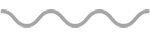
Extra Cleaning Work
All objects should be free from paint, lacquer, grease, oil or other protective layers that cannot be removed by common acid pickling. Costs of removal of such coatings, old zinc coatings, and also extra hard rust and iron scale are charged extra. Any regalvanizing of objects, which have to be treated again in spite of preceding attempts at cleaning, will also be charged extra
Welds and Other Joints
All welds from the customer should be cleaned free from slag, as it cannot be removed by pickling. The remains of slag on the welds – including coatings on welds performed with protective gas – will cause stains in the zinc coating, for which the galvanizer cannot be held responsible.
Neither can the galvanizer be held responsible for stains and rust owing to remains of pickling acid in leaky welds or narrow spaces, e.g. between surfaces which have been bolted together or riveted.
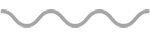
Defects in the Parent Metal
For defects in zinc coating owing to roller defect, slag or other defects in the parent metal, e.g. moulding sand in castings, or for cracks in castings coming into existence during immersion in the solution of zinc, because the object has latent stresses or unlike material thickness, the galvanizer cannot be held responsible.
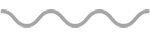
Deformations
For deformations and twistings owing to stresses in the object, the galvanizer cannot be held responsible, and any special arrangements to prevent, this, e.g. preheating, will be charged extra.
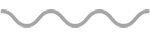
Changes of the Material
The customer bears the risk of changes in the material of the object, e.g. ageing or other shortness owing to the reaction of the material during the treatment, cf item 1. Special attention must be paid to the fact that in case of hot dip galvanizing of steels with tensile strength exceeding 1000 N/mm², hydrogen shortness may appear. Attention must be paid to the fact that flame/plasma or laser cutting of edges will affect the contents of silicon, for which reason the galvanizer does not guarantee coating thickness and adherence on these.
Steel Type
Colour, appearance and thickness of zinc coating depend on the reaction between zinc and steel during hot-dip galvanizing process. That, on its turn, is determined by several factors, mainly the composition of steel, characteristics of its surface (structure, porosity, internal tension, and roughness); reaction is influenced by composition of molten zinc, immersion duration and other factors.
Majority of these factors cannot be influenced by hot dip galvanizer. Most suitable for hot dip galvanizing is steel with silicon (Si) content of 0.0 – 0.04% or 0.15 – 0.25%, as well as with aluminium (Al) content up to 0.02%. Non-suitable steel content may result in too thick and non-persistent zinc coating.
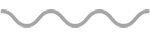
Venting tubular fabrications & hollow structurals
If closed hollow spaces are immersed in a hot solution of zinc, there is a risk of violent and highly dangerous explosion because of the sudden evaporation of unexpected confined fluid. Vessels, closed vats, barred hollow spaces, hollow construction parts, e.g. in pipe constructions and the like, and also spaces between surfaces welded together, have to be bored for scavenging and outlet. In case the object has contained an inflammable substance, it must be cleaned totally free from this, or else it might catch fire or explode. Each part may require clamping holes, if no suitable place for clamping can be found. Boring of holes will be charged extra. The decision of the placing of the holes requires special technical knowledge and should be made by the galvanizer or prearranged with him. The galvanizer makes reservations of galvanizing of closed profiles, so we cannot be held responsible for damages on the zinced product or damages which this might cause, due to internal corrosion of the profile, as we call attention to the fact that remains of ashes might occur inside the pipes and will not be removed by us. Along with moisture these remains of ashes might be corrosive.
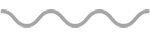
Packing Flanges, etc.
Unless otherwise agreed, the galvanizer does not take upon himself to deliver and mount packing flanges, scavenging pipes, protection muffs and the like. Such services are charged extra and performed without responsibility.
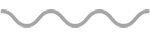
White Rust
White rust is white, powdery deposit (zinc oxides formed through zinc corrosion). It forms rapidly on the surface of freshly galvanized coatings that are nested together, tightly packed, exposed to high air humidity or rain and are insufficiently ventilated. Corroding reaction continues as long as there is moisture on the surface of the steel structure. Reaction ends when air access is ensured for all surfaces of the steel article. White rust is no cause for rejection.